It reinforces the concept everyone within the organization is answerable for quality, not simply the testing or high quality department. In easy phrases, quality assurance is all about planning and establishing processes related to high quality. The distinction between these two methods may be fairly blurred, however their understanding and effective quality assurance vs quality control implementation are pivotal to any business that goals for sustainable growth and a high quality buyer experience. High Quality management is just like assurance, though it measures the standard of particular person goods made through mass manufacturing.
Quality Assurance is a proactive approach to preventing defects and ensuring that quality requirements are persistently met. A well-implemented QMS helps coordinate and direct an organization’s actions to meet buyer and regulatory necessities and enhance its effectiveness and efficiency on a continuous foundation. QC is commonly used after the manufacturing or service delivery process to examine and take a look at React Native the ultimate products or services. QC, meanwhile, entails the testing of merchandise to ensure they meet those requirements for safety and efficacy. If QC testing uncovers high quality points, it ought to end in reactive steps to stop an unsafe product from being shipped and distributed.
Its main focus is on figuring out and correcting defects via inspections, testing, and evaluations to ensure the final output meets the specified standards. Whereas QA focuses on preventing defects via the usage of correct procedures and processes, QC ensures that the ultimate product is free from defects and meets your high quality standards. High Quality Control is a reactive process that focuses on figuring out and eliminating defects in a completed services or products.
What Are The Variations Between Quality Management, High Quality Control And Quality Assurance?
It focuses on identifying and addressing defects or quality points in finished products, in order that they match specs. Good quality assurance and quality management are two of crucial parts of a successful operation in numerous industries, corresponding to manufacturing and engineering. Attaining, ensuring, and maintaining the standard of your goods and providers are paramount to making your prospects happy and hold them coming again. Study about quality assurance and quality management, their differences, and the three quality assurance and quality management methods you should use to boost your high quality standards and practices. Professionals on this subject have the opportunity to contribute ideas that can result in the event of new merchandise, companies, or processes, making a meaningful influence on their organizations. As industries focus more on maintaining high requirements and compliance, the demand for high quality management professionals continues to grow.
Major Differences Between Quality Assurance And High Quality Control
It consists of steps like defining requirements, creating guidelines, and conducting audits to make certain that the defined procedures are being followed. Quality Assurance is popularly generally known as QA Testing, is defined as an activity to guarantee that a company is offering the very best services or products to prospects. Project administration uses quality management to discover out whether or not a project has met the agreed-upon standards set by the client or the company. In these circumstances, the time period has a slightly completely different that means, as the end outcome is not compared to an preliminary prototype or manufacturing run. High Quality assurance requires planning, testing, and monitoring to realize its aim. Then, the manufacturing process is monitored to ensure the requirements are followed strictly.
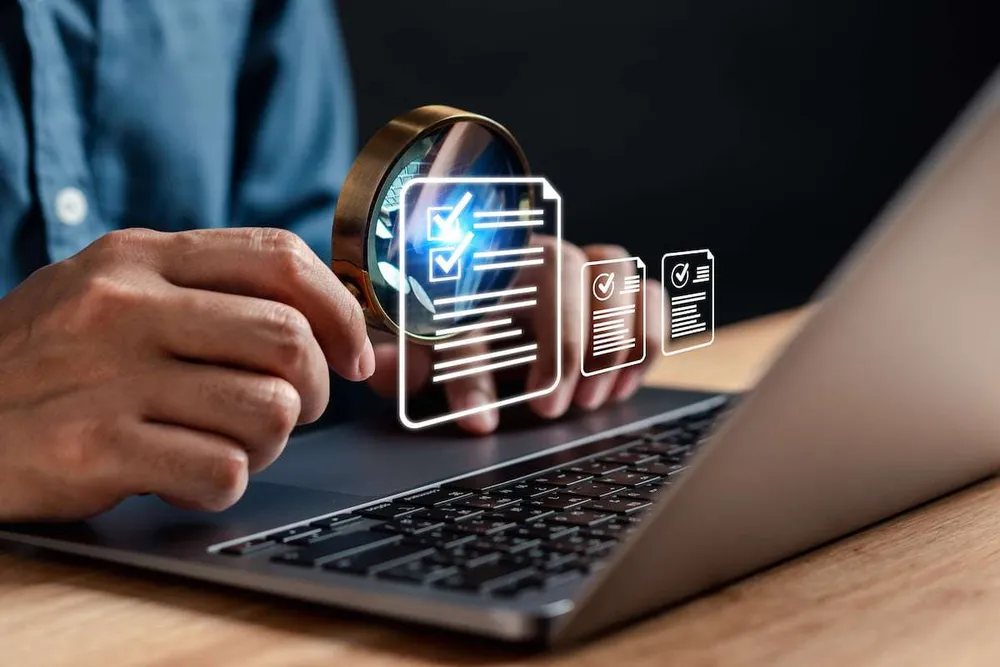
Whereas QA can modify approval and risk assessment workflows, QC can tailor inspection schedules, customise form templates, and extra for better productiveness. It serves as a centralized platform for both QA and QC teams to determine and log incidents and implement effective corrective and preventive measures for immediate and long-term improvement. Both QA and QC depend on effective documentation and standardization to achieve their desired results. An digital High Quality Administration System (eQMS) streamlines both QA and QC by automating workflows, making certain compliance, and offering real-time visibility.
- Understanding methodologies similar to Six Sigma, Lean, or Whole High Quality Administration (TQM) can significantly enhance a QA professional’s capability to improve processes and remove waste.
- High Quality management in manufacturing isn’t exactly the identical as within the software trade.
- If you have a ardour for quality, problem-solving, and continuous enchancment, this subject can present a satisfying and rewarding career path.
- As An Alternative of checking every single unit, sampling includes choosing a consultant batch for inspection or testing.
QC, however, is concentrated https://www.globalcloudteam.com/ on the specific activities that detect and correct defects, often on the proverbial coalface just like the meeting or manufacturing line. These are questions on your high quality management system to take care of – not high quality assurance. In practice, then, QA means things like developing standard operating procedures (SOPs), conducting audits, verifying and validating processes, and training workers. Follow these 12 important steps to successfully implement OHSAS inside your organization and enhance office safety administration and threat mitigation. With the mixing of those aspects, you can uphold excessive requirements, reduce dangers, and consistently exceed expectations, fostering trust and long-term success in competitive markets. This article will discuss high quality management and assurance, why they’re important, how they work, and the difference between high quality control (QC) and assurance (QA).
Improved Product Or Service Quality
While not solely a quality framework, Lean strongly overlaps with QA and QC practices by emphasizing course of optimization and defect reduction. Steady enchancment retains your quality systems agile, helps adapt to market adjustments, and strengthens your competitive position. The stronger and extra supported your quality administration system is, the extra you’ll be able to secure company-wide buy-in and consistent commitment to all of the types of high quality exercise you need. In a robust and optimized high quality management system, high quality control should solely kind a small a part of your total activity – say, 25-30%.
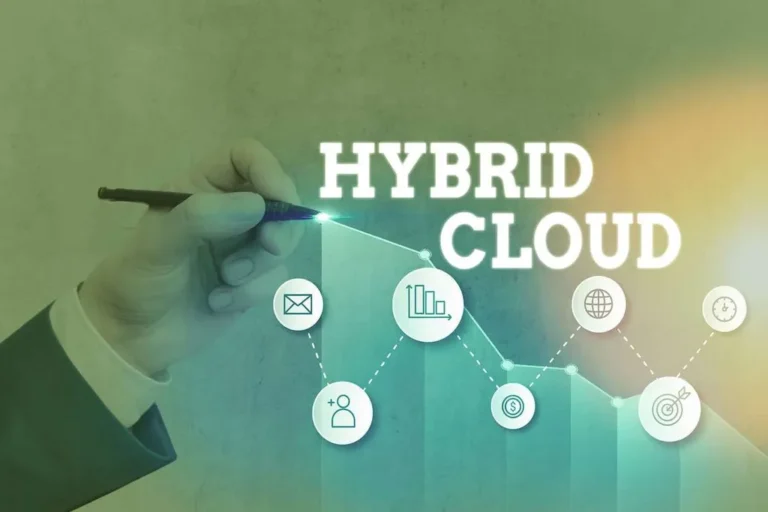
While QC focuses on identifying and rectifying defects in finished merchandise, QA proactively establishes preventative measures all through the complete manufacturing process. This twin technique ensures consistent supply of high-quality products by building a robust framework that minimizes errors and maximizes efficiency. By investing in both QA and QC, manufacturers reveal a dedication to excellence and buyer satisfaction, in the end leading to a competitive advantage out there. Quality assurance (QA) is a set of actions and procedures, also recognized as quality requirements, that take place during and after product growth.
Quality control (QC) and quality assurance (QA) have totally different roles and purposes inside a quality management system. The decision to use QC or QA is dependent upon the specific wants and objectives of your group and the stage of your product lifecycle or service delivery. It requires a commitment to continuous enchancment, common analysis of outcomes, and the flexibleness to adapt to altering circumstances and buyer expectations. They have 1000’s of manufacturers to choose from and may entry millions of shops as a outcome of advances in know-how. If the model does not meet the shoppers’ expectations by way of the worth supplied, the revenue will be at stake, too.
QA pointers also maintain projects in scope and on monitor by aligning team members on collaboration practices and strategies, similar to code evaluations in software development. Both methods work collectively to determine alternatives for improvement, although there are differences within the role of high quality assurance vs. quality control. When QC processes determine recurring issues, QA processes use that information to regulate systems and stop the problem from occurring again. This continual cycle of studying and enchancment promotes a proactive culture of quality inside a company.